Page 1 of 2
Billy's LH mudguard - Repairing corroded tinwork
Posted: Mon May 31, 2021 12:05 am
by Billy26F5
Billy's LH mudguard suffered corrosion damage due to lack of cleaning and being in the damp, the box sections finally giving way in 2006 (I think). Since then it's been loose bouncing around after every bump, but this weekend we finally got round to doing it. The first job was to tack the rear box back on, a jig was made up to hold the mudguard in exactly the right place by clamping two bits of wood using the other mudguard as a guide and using a stick on the other side as a wedge (note only machined parts are being used for the jig to settle on).
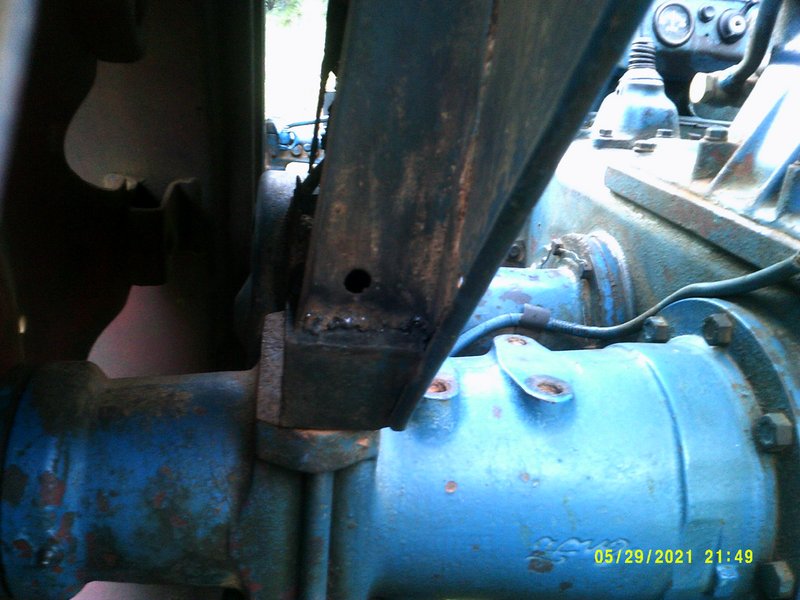
Once that was done the mudguard needed to come off. The wee bolts came off easily enough, but the main bolts were pretty stiff (it took about three hours to loosen the nuts and another two to get them out altogether). The side light wire was burried in hardened dust, which needed to be ploughed out of the way in order to get it out. The connector screw came out very easily surprisingly.

Here's a shot from 1998, to show that it was already needing attention, but it still felt solid then (and partly supported the axle casting when it was removed in the rear end overhaul then)
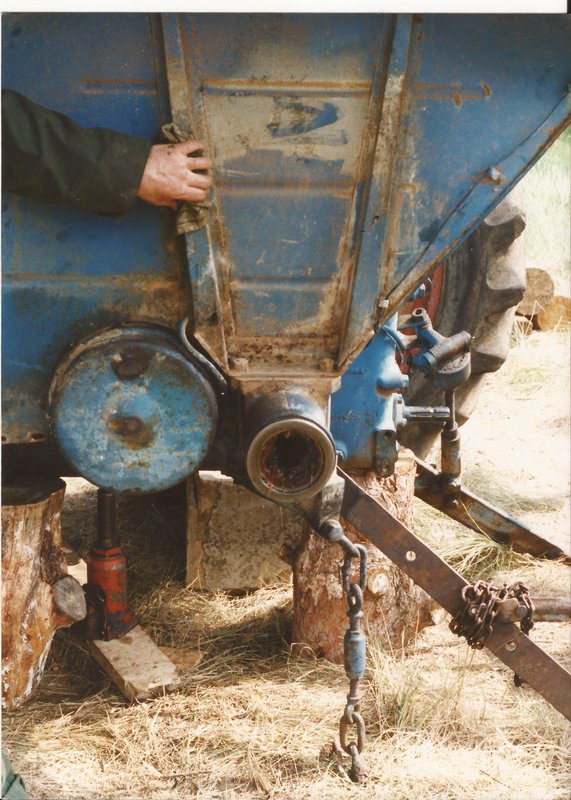
And some from the next morning after removing the mudguard, showing the extent of the damage.
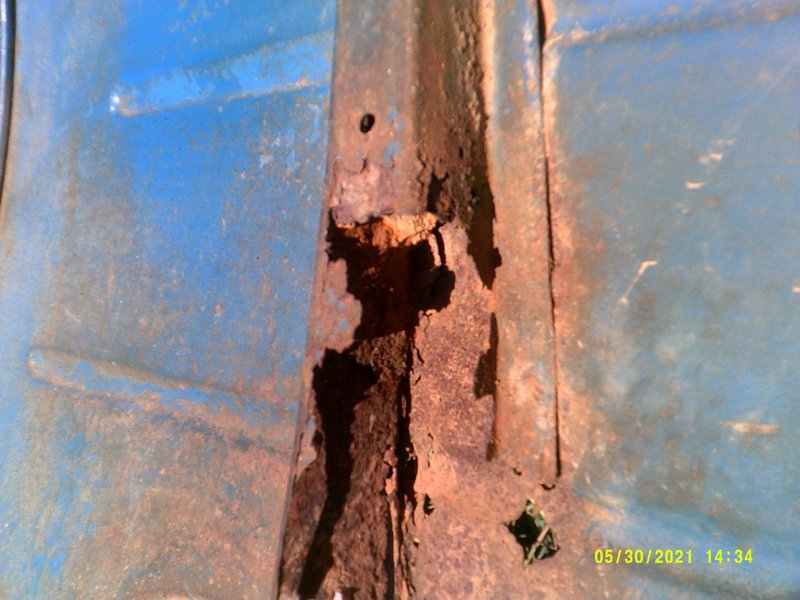
With the bolts now out cleaning can begin. The bolts will be refitted and tightened to ensure no damage to the check chain bracket if we need to do something in a hurry (hoping that's not the case though, as it's a bit exposed!)
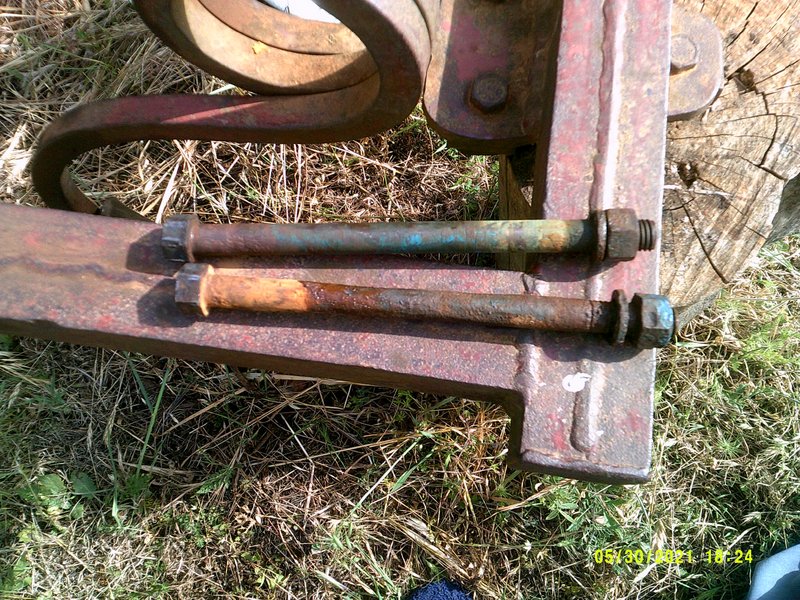
Now proper welding can begin, note this is only my second ever welding session!
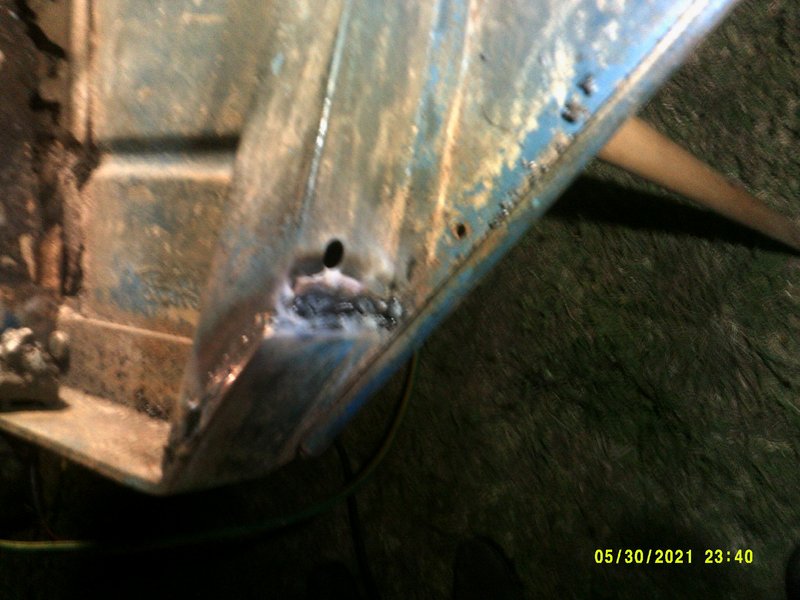
That's that for now. More to come soon.
Sandy
Re: Billy's LH mudguard - Repairing corroded tinwork
Posted: Thu Jun 03, 2021 11:40 pm
by Billy26F5
Re: Billy's LH mudguard - Repairing corroded tinwork
Posted: Fri Jun 04, 2021 7:32 pm
by henk
Lots of careful welding to do. Should be a lot easyer to use MAG welding. But then you need other equipment.
Re: Billy's LH mudguard - Repairing corroded tinwork
Posted: Fri Jun 04, 2021 10:18 pm
by Billy26F5
Unfortunately we only have an old std arc welder, we're using it on low power thinking that will stop it becoming a crude plasma cutter, but we may be quite wrong, although in most cases we've managed to avoid damage so far. The front box will be more delicate, as it's quite thin in places.
Another report coming soon.
Sandy
Re: Billy's LH mudguard - Repairing corroded tinwork
Posted: Sat Jun 05, 2021 1:55 pm
by Old Hywel
I notice grease nipples ‘fore and aft’ on the axle. Is this usual?
Re: Billy's LH mudguard - Repairing corroded tinwork
Posted: Sat Jun 05, 2021 3:12 pm
by Billy26F5
It is normal with the castings from this era (1955). They changed later to have only one at the back (I don't know exactly when, but I think all Super Major's have the later casting). If anyone has some confirmed dates of the change we can then see when the change occurred (casing codes on some of the earlier axle castings are a bit difficult to read).
Sandy
Re: Billy's LH mudguard - Repairing corroded tinwork
Posted: Sun Jun 06, 2021 10:41 pm
by Billy26F5
Re: Billy's LH mudguard - Repairing corroded tinwork
Posted: Mon Jun 07, 2021 7:19 am
by mathias1
I know they sell new fender supports to weld on.
I think your welding will need some practice, not that I am that good at it. Is your current adjusted to the stick you use?
Re: Billy's LH mudguard - Repairing corroded tinwork
Posted: Mon Jun 07, 2021 7:56 am
by Billy26F5
We're so inexperienced that we don't even know that! We're trying to keep as much original material as possible, which makes this more difficult. Our welding will need lots of practise, for now it still feels like something odd to be doing, as we haven't really done very much at all.
Sandy
Re: Billy's LH mudguard - Repairing corroded tinwork
Posted: Wed Jun 09, 2021 5:16 am
by Old52
Hi Sandy:
If you look on the web you will be able to find a chart that shows approx amperage range for the thickness of the metal and the type of stick you are using (i.e. 6013 or 7018) stick wellding thin sheet metal is tricky at the best of times, but a small rod and lower amps should do it. Good luck.
Bob
Re: Billy's LH mudguard - Repairing corroded tinwork
Posted: Wed Jun 09, 2021 7:55 am
by Billy26F5
Thanks very much Bob. We're using 1/8" rods (all we've got), our welder doesn't actually say any current, there are ten connectors numbered 1-10, part of our problem is that the welder is from a friend and we don't have any instruction books or similar on it which means we're a bit more lost than we might have been.
Sandy
Re: Billy's LH mudguard - Repairing corroded tinwork
Posted: Wed Jun 09, 2021 4:26 pm
by Old52
Do you know what type of rod you are using? 1/8th rod is big for that thickness. Also, if the rod is old and not dry, that will make it much harder. Try practicing on some thicker material and play with the welder settings...
Good luck.
Re: Billy's LH mudguard - Repairing corroded tinwork
Posted: Wed Jun 09, 2021 6:48 pm
by John b
Hi Sandy, trying to keep as much original material as possible may cause you more grief than you need. Stick welding thin steel is hard enough but any trace of rust or paint near your weld will make it almost impossible.i taught myself to weld so i learned the hard way, i wish youtube had been around 35 years ago, the tutorials on there make things so much easier! If your welding rods haven't been stored in a dry, airtight container pop them in the oven for an hour, they'll work alot better. If you have holes in the thin mudguard tin you will have to cut out all the rust and weld a patch over them, you could try welding a piece of metal into hole you have cut out but its not easy with a stick welder (i'm talking as an amateur welder here, i'm sure there are plenty of pros who could do it). I take my hat off to you for having a go but be careful, its so easy to get into a real mess, when i was 17 i decided to weld up a small hole in my viva wing, the hole got bigger and bigger and i ended up having to fit a new wing!
John
Re: Billy's LH mudguard - Repairing corroded tinwork
Posted: Wed Jun 09, 2021 9:32 pm
by Billy26F5
Thankfully the hole hasn't grown more than about 1/16" outward. It feels quite solid enough (it's just a mudguard, not an important bit for strength), so we'll see how it goes. We're doing this on the lowest current setting on the welder (the setting marked 1, I think our electrics would cut out at max current) thinking it would avoid any unwanted melting. At the moment our main problem is that the metal forms blobs in a sea of slag, but I'm not sure what that means. If this doesn't work we'll fit new material, but at the moment I remain hopeful that it might just hold on and allow us to finish it sooner, as we'll need to do some ploughing very soon. Tomorrow we'll see if after grinding it survives. We're hoping to get a better idea of welder settings on our J Bargans trailer, that needs fixing too.
Sandy
Re: Billy's LH mudguard - Repairing corroded tinwork
Posted: Wed Jun 09, 2021 9:55 pm
by John b
Stick at it and you'll get there, welding is one of those jobs where you can be shown how to do it but the only way to get it right is practice and get the 'feel' of it and get used to the welder. Good luck
John
Re: Billy's LH mudguard - Repairing corroded tinwork
Posted: Fri Jun 11, 2021 11:17 pm
by John b
Heres a tip i was shown by a bodywork repairer, make yourself some copper 'spoons', if you re trying to fill a small hole with weld, hold the 'spoon' flat against the back of the hole while you weld, it will stop the molten metal running straight through and it won't stick to the coppper
John
https://app.photobucket.com/u/Dixienormous68
Re: Billy's LH mudguard - Repairing corroded tinwork
Posted: Sat Jun 12, 2021 7:35 am
by Billy26F5
Thanks very much John. Unfortunately we're a bit short on copper, but we'll try and see if we can make them and try them.
Sandy
Re: Billy's LH mudguard - Repairing corroded tinwork
Posted: Sat Jun 12, 2021 9:45 am
by John b
If you have any offcuts of copper pipe anywhere i've used them before now, just hammer one end to the shape you need and bend the rest to form a handle
John
Re: Billy's LH mudguard - Repairing corroded tinwork
Posted: Sun Jun 13, 2021 10:24 pm
by Billy26F5
Re: Billy's LH mudguard - Repairing corroded tinwork
Posted: Mon Jun 14, 2021 12:01 am
by John b
Hi Sandy, did Ford supply the tinwork to Ebro, or did Ebro use the original Ford jigs?
John
Re: Billy's LH mudguard - Repairing corroded tinwork
Posted: Mon Jun 14, 2021 12:20 am
by Billy26F5
Billy is a Major (with a much later Ebro engine). Until the Power Major, Ebro simply re-badged Majors, after that they used their own tools (for everything); later Ford sold them theirs (1965). Billy has picked up other Ebro bits, like the side lights.
Sandy
Re: Billy's LH mudguard - Repairing corroded tinwork
Posted: Mon Jun 14, 2021 12:37 am
by John b
Ahh now it makes more sense, wasn't too sure of the Ebro history
Cheers
John
Re: Billy's LH mudguard - Repairing corroded tinwork
Posted: Thu Jun 17, 2021 11:16 pm
by Billy26F5
Re: Billy's LH mudguard - Repairing corroded tinwork
Posted: Sun Jun 20, 2021 9:59 pm
by Billy26F5
Did a bit more today, with the new grinding disc, it's much better than the other one was (and noisier too!).
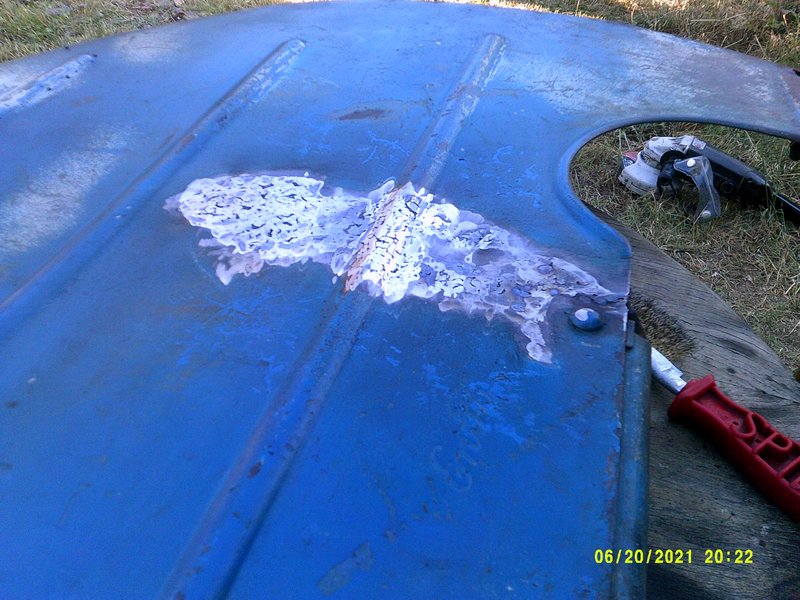
Only a few holes there before moving on to the other side!
Sandy
Re: Billy's LH mudguard - Repairing corroded tinwork
Posted: Thu Jul 01, 2021 10:54 pm
by Billy26F5